One of the core aspects of the art of lutherie is understanding wood on its most basic levels. Everything from the cell structure to grain spacing, grain orientations, growth patterns, density, and more, are on my mind as I look at a potential piece of wood for a component of a guitar that I’m working on.
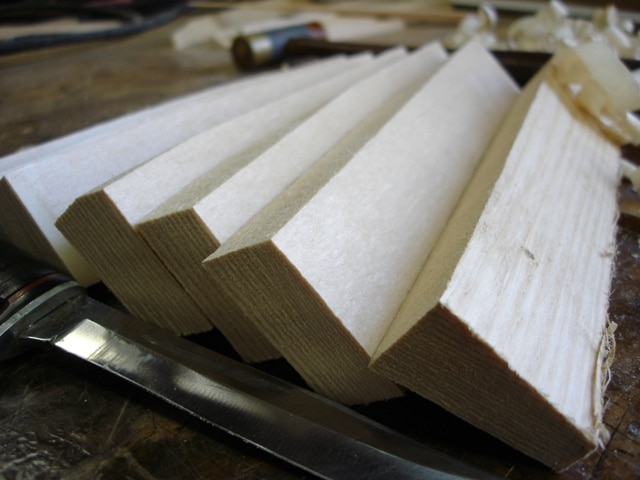
Some of the most critical components on the guitar to select wood for are the tone bars. These small bars or braces, usually made of Spruce, enhance the structural integrity of the guitar top as well as function to shape the behavior of the top as it is in motion, thus setting the tonal parameters of the guitars voice by limiting certain frequencies and encouraging other frequencies to vibrate more easily.
When selecting wood for these elements it is vitally important to be sure that you know exactly how the strength and flexibility of each piece is behaving. What I’m after is consistency, I want to be absolutely sure that each tone bar is as consistent as possible from end to end. The amount of variation from piece to piece never ceases to amaze me, even if they were side by side in the tree.
I also created an online course on this subject in case you wan to use this technique on your guitars, it is called: The Art Of Splitting Braces By Hand. It is part of the Luthier’s EDGE Online Luthier School. You can use the links above or scroll down this page to check out the video for more info.
Hand Splitting Spruce Tone Bars
If we want the highest stiffness to weight ratios and evenness of tone possible, the above mentioned variations present in most wood make it critical to hand split the wood for the tone bars.
By splitting the wood you get to see how the wood breaks along its natural growth lines. This will reveal many things such as grain run-out, twist, knots, and other secrets of the wood that would go totally undetected if the tone bars were simply cut out of a block of wood with a power tool.
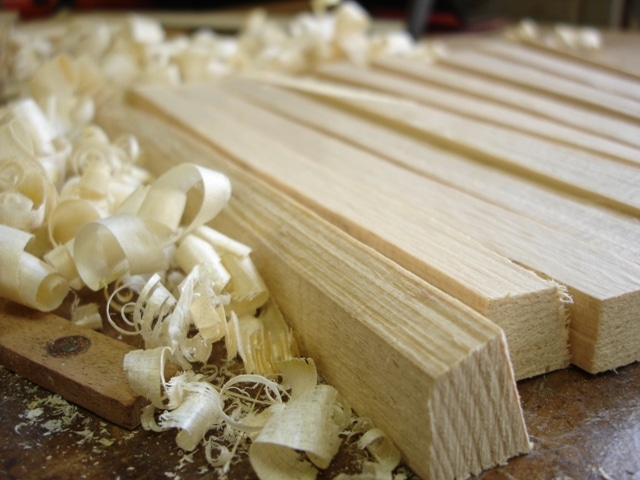
Fine Tuning
Once I have the wood split to a close enough tolerance, I then use my hand plane to bring them down to the final rough dimensions. I also do further fine tuning to be sure I have the absolute best quarter cut grain orientation and that the grains will run perfectly parallel with the center line of the bar. If either of these two things are out even a small degree, it has an enormous effect on the bars strength and consistency.
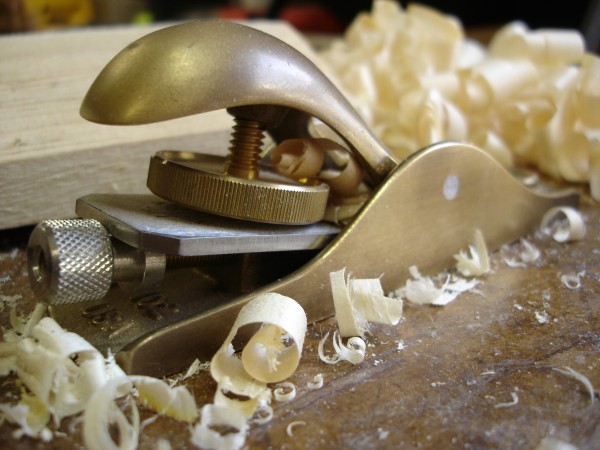
Strength and Tone
Now that I have all the bars split and fine tuned to my rough dimensions, I can test each bar for strength and tone. I test the tone by dropping them one by one on a steel table, listening to the sound they make as they hit. I might also sometimes hold them like a drumstick and tap the ends to hear the sound they create. I make notes of this data and then I flex each bar individually, sorting them into groups from stiffest to weakest.
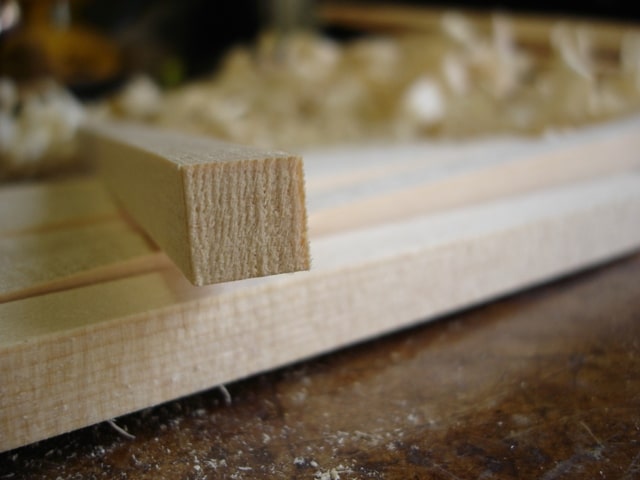
Building For Tone
From there I choose which bars will work best in the design I’m working on. It is not always the same, there is no formula, the critical thing is that with this method I can be sure that my bars are totally optimized for strength, consistency, and tone. I can also be confident that I’m adding the right ingredient into the design to achieve the desired tonal and structural outcome.
Check out this video to learn more
HI Tom,
Love your view on wood and your intense thoroughness. I have a general question that I’m sure is not necessarily easy to answer and that is. Does the stiffer tone bar produce a louder more bright tone?
Thanks!,
Mark
Hey Mark,
Thanks for taking the time to comment and for your kind words!
That is a good question, I’ll do my best to answer according to my experiences. I think that my approach regarding tone as pertaining to the tone bar selection is more focused on the density of the piece and the final shape or cross section of the brace.
I drop different woods onto a steel table and listen to the sound they make, its a good indicator of which pieces will add brightness or other characteristics to the recipe you are creating in a specific guitar. The cross section of the finished brace does also seem to effect the tone quite a bit. A taller thinner brace, kind of fin shaped, will give a brilliant sound and a lower rounded or bullet shaped brace will be a warmer sound. So you can use those parameters to fine tune things regarding your tone bars.
The stiffness is desirable not so much for tone, but for efficiency. The stiffer it is, the thinner I can make it and the lighter it becomes. The less mass there is, then it will take less string energy to set things in motions, thus resulting in a louder and more responsive guitar. I go into great detail about this important concept in the course about Guitar Physics.
Let me know if you have any more questions, thanks!
Tom
Hi, Tom I admire the way your site teaches and motivates,great job.
Ive been a guitar maker for 25 years and yet never have made an archtop,but thats changing,this year will be the year.
Ive searched but cannot find any real info on what the size and shape an f hole has on tone .many first timers just copy an existing one but id like to know what Im doing before choosing ,designing or madding an f hole shape .Id love to hear your thoughts on f holes
Hi Greg,
I will have to write an article about that; it’s a big and important subject. I address it in detail in my new book/DVD set that will be out soon published by Mel Bay. I’m sure I’ll write about it when it’s released so be sure to sign up for the mailing list here, and you will know when the book is out.
Also try to find a GAL book called Luthier Woods and Steel String Guitars, it has a very controversial article by Jimmy D’Aquisto in it which among many other things focuses on the shape and size of the sound-hole and the affect they have on tone. https://www.amazon.com/Lutherie-Woods-Steel-String-Guitars/dp/0962644714 page 50. A must have for any archtop guitar builder!
Tom
Hi Tom, Thanks for all the teachings, and your book is great. I have an archtop mandola with a wolf tone on the outer G string. Can’t shake it. Your book details this well, but I am seeking a strategy for correction. I understand I need to change a resonant frequency on one of the plates? I would rather remove material from the back than the top. What would you recommend? Thanks again you have taught me a lot!
Hi Keith,
I am so glad you found the guitar making book helpful, thanks for giving me some feedback on it!
Sometimes those wolf notes are hard to track down. Before you start removing wood, try adding some weight to different places on the top, to see if you can locate the spot where that frequency is dominating. Just maybe use some magnets (one inside and one out) or even a small weight temporarily taped in place…or whatever you can come up with that won’t hurt the instrument. Move around on the top or the back and look for that spot. If you find it, maybe you can glue a small weight inside to add some weight to that place and diminish the wolf note.
I recommend this because sometimes you can increase the wolf note by removing wood and then you can really have a hard time.
Thanks again!
Tom